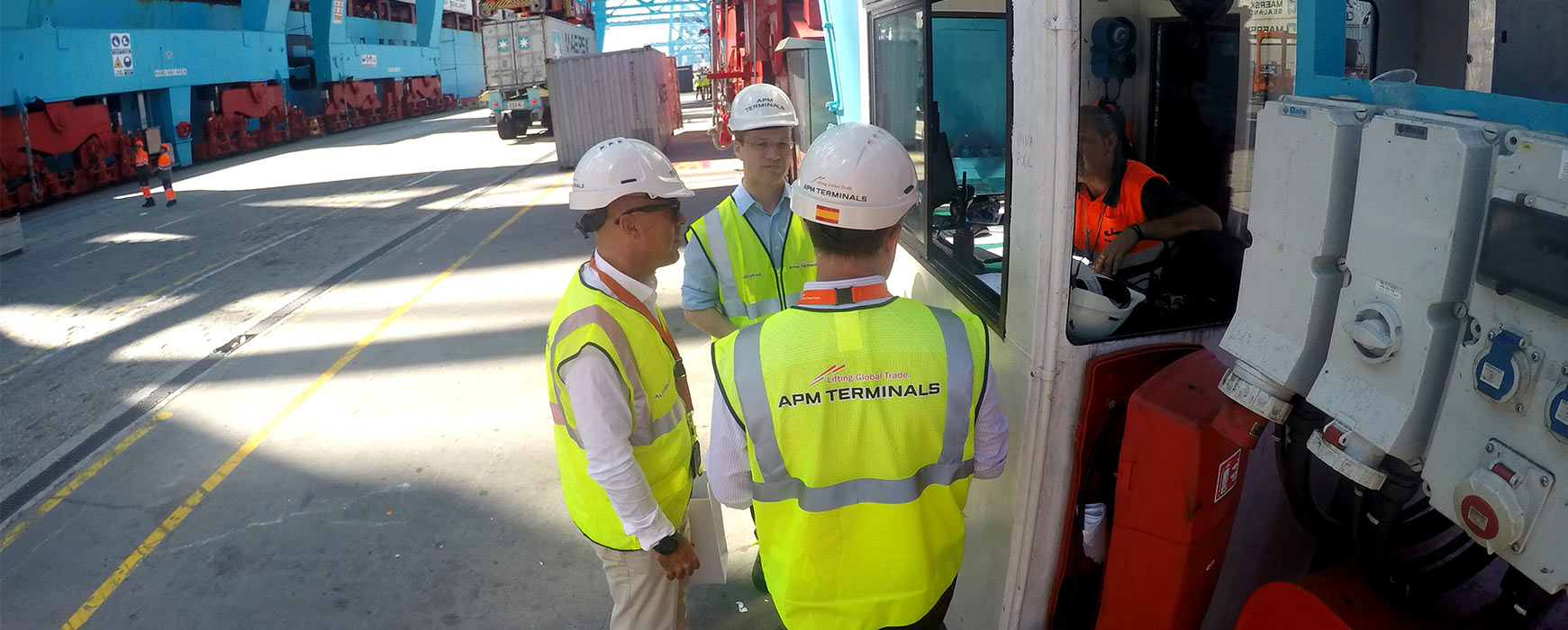
30/04/19
Global Safety Day marks a shift in safety philosophy at APM Terminals
APM Terminals’ focus for this year’s Global Safety Day is ‘Learning from the way we work’. This is part of the company’s shift from traditional safety – which focuses on outcomes – towards ‘Safety Differently’, which focuses on understanding and improving normal work processes to improve safety performance.
In support of Safety Differently APM Terminals is implementing ‘Learning Teams’ to ensure its employees’ knowledge and experience about safe working is used effectively.
“Our employees working on the quayside, at container freight stations, and in warehouses and storage facilities to mention just a few, are the people with the highest injury potential,” says Ruth Gallagher, Global Head of HSSE Improvement at APM Terminals. “Our management have more influence over work design control and yet hold the least knowledge about how the daily work is done. Learning Teams will close this gap.”
Learning Team philosophy
The Learning Team philosophy is that the employee or worker is the solution, and not a person to ‘fix’ because they deviated from standard controls. “My role is to drive a shift in mindset to help us learn from workers on the front line and ask them to develop the solution,” she says. “Learning Teams are about building trust, not blame.”
At APM Terminals, the Learning Teams established on Global Safety Day will be used to answer questions such as, ‘If work processes are time-sensitive, how can the company provide the necessary time to achieve the goals without slowing down the processes?' Or, ‘If front-line staff have to deal with complicated or unrealistic procedures, how can those procedures be changed to make them workable?'
The concept is currently being trialled by APM Terminals with Learning Teams focusing on lashing safety. The job of lashing and securing containers remains largely manual and is a hazardous operation. Across APM Terminals’ operations last year, lashing injuries were the cause of more than 35% of all global incidents where a person was unable to return to work the next day. With vessels calling at its terminals growing larger, the risk of injury for lashers remains high.
Gembutsu approach
Leadership at a number of terminals were asked to complete GEMBA walks for lashing. The term GEMBA originates from the Japanese term gembutsu, meaning ‘real thing’. It is the term used to describe personal observation of work and is closely tied to the concept of Learning Teams and a fundamental part of APMT’s operating system. The focus of the walks was to see the process and validation of controls in action. During the walks, leaders held discussions with lashing teams to understand how to keep them safe.
Tools and tips have been developed to help leaders get the most out of the walks and an online survey tool records outcomes and supporting images. The walks helped achieve a better understanding of the tasks involved and identify improvements, which can then be shared with other terminals. The outcome also demonstrated an increased sense of ownership of the solution, which make any improvements more effective overall.
Proven effectiveness
With over 240 GEMBA walks now completed, the initial response has confirmed how effective this approach can be. For one leader, it was an opportunity to reinforce the company’s ethos that they will never put productivity before safety. According to Gallagher, “This type of message, coming directly from leadership at the very moment the stevedoring team have to make a call, has so much more impact than a safety discussion in a board room could ever have.”