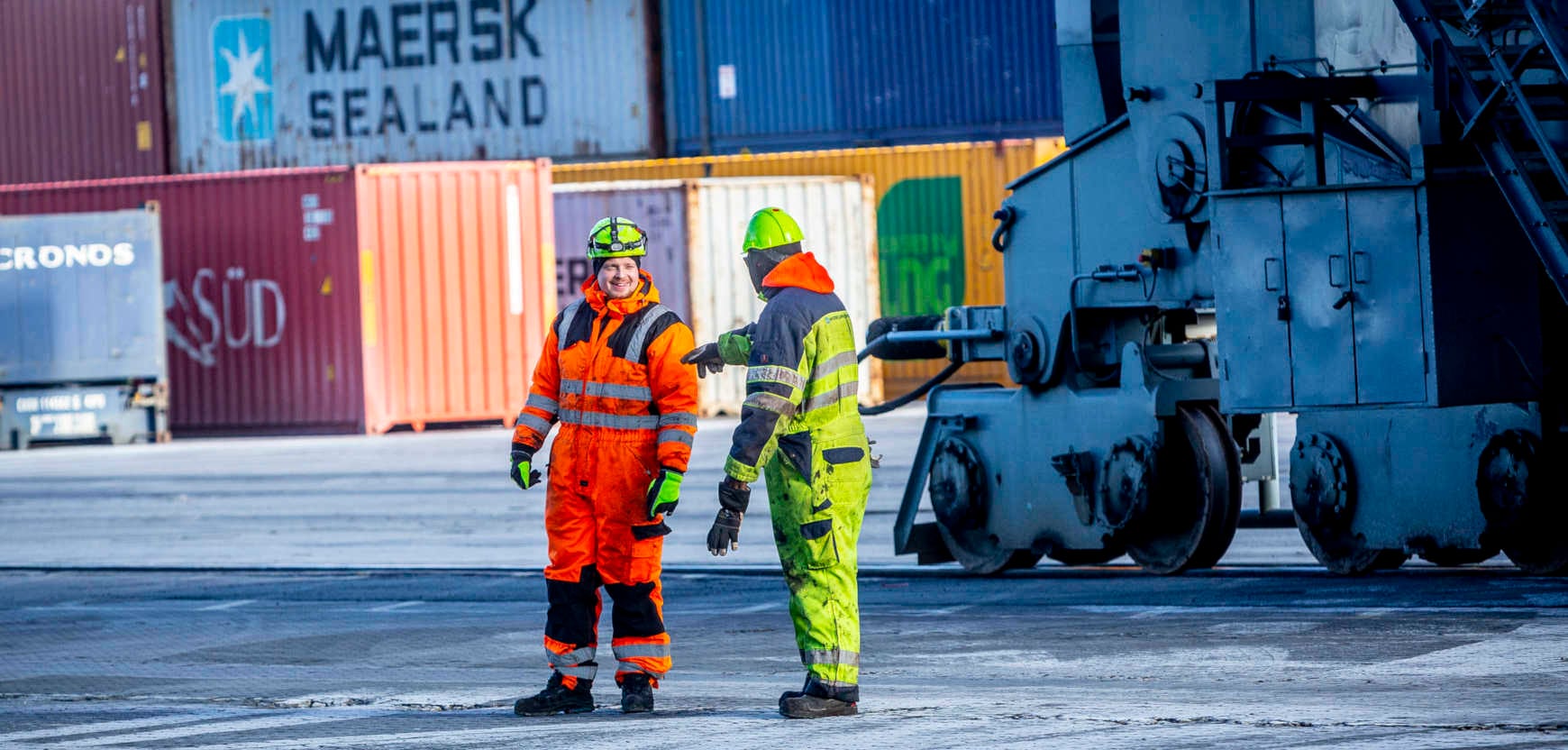
14/04/21
Blog: Strengthening our safety culture through Way of Working - by COO, Keith Svendsen
At APM Terminals, the safety of our people is our first priority. Over the years, we have made real progress in reducing the number of accidents, but too many people still get hurt. We are deeply committed to closing this gap, so that everybody can come home safe every day.
To solve this problem, we have decided to leverage our colleagues and our LEAN methodology toolbox. We are encouraged with the progress we are making on making APM Terminals safer and how we are embedding safety deeply into our daily work. There are some early changes we have made which are already bringing results.
First, giving our people the power to change and improve their work processes (standardization) and environment creates a safer and more engaged workplace. Secondly, we have set clear expectations for our leaders that it is crucial in their role to get involved in the details of the standard daily work of our frontline people and to perform daily Gemba walks (from Japanese: “the real place”; going to the real source). This has created positive touchpoints, removed obstacles and accelerated improvements in work processes and training.
Walking the talk
At APM Terminals Tangier in Morocco, we have been piloting a number of solutions with tangible results. The local team understood that in order to drive the “leader led” mindset across their terminal, they needed “every brain - and heart - in the game”. In order to drive engagement and increase the understanding of work done between the frontline teams and leadership, they needed everyone to “walk the talk”.
Gemba walks have become fully integrated into the terminal’s Way of Working (WoW), with every leader performing at least one Gemba walk per week. The Terminal Leadership team consider these touch points an opportunity for their leaders to see how our processes and safety controls are implemented at the actual place of work. This brings leaders and front-line teams together in an environment where they actively listen and explore how effective processes are, what works well, what is difficult and what can be improved. It is also an opportunity for leaders from all levels to understand operational risks, challenge their thinking and work with front line teams to improve safety performance.
More empowerment
Gemba walks are supported with the use of a leader led app which captures observations and learnings from the walk and the discussions. The data is then analysed and embedded in the terminal’s weekly performance meetings. This is translated into corrective actions or “Kaizens”). In 2020, 50% of the terminal’s Kaizens were safety related and could be directly linked to Gemba walks. Getting a little better every day makes a big difference over time!
To build engagement and embed lean thinking, they trained 100% of employees on the basics of LEAN methodology, with a strong core of 18 Lean coaches at advanced level 5 (it is a 6 step model) to support the organisation and empowered them to use these skills to generate improvement ideas and create a safer workplace. They have also involved front line teams to own and create their work instructions, which are validated through peer or supervisor training using TWI methodology for all core activities with safety controls embedded. Pictograms of key activities or controls have been created to visually distinguish safe from unsafe actions, connecting across our teams to build confidence, competence and capability to deliver a safe working environment for everyone across the terminal.
Recap of learnings – Steps to Success
- Visualize all problems and then build teams capable of solving them;
- Simplify and visualize work instructions – built by people for people with safety in mind;
- Get leaders to the workplace through Gembas to understand the reality of work and to build engagement and feedback from frontline teams;
- Give teams a voice and purpose to address safety hazards when they come across any;
- Empower employees by giving them the skills and problem solving tools to have the best chance of success, and make changes to their work and environment;
- Instil a positive learning approach that balances learning across successes and mistakes;
- Drive improvement and learning through embedding leading and lagging Daily Metrics;
- Drive the right conversations at the right time, without fear or hierarchy, aiming for the right impact – rather than chasing “green” KPIs;
- Exploit technology to eliminate risks, simplify processes and remove administrative burden;
- Repeat to build and sustain performance.
Newsletter Subscription
We'll only send you our Global Newsletter when we've got something we're confident you'll be interested in. Simply enter your details via the link below and select the Global Newsletter box on the Newsletter tab.